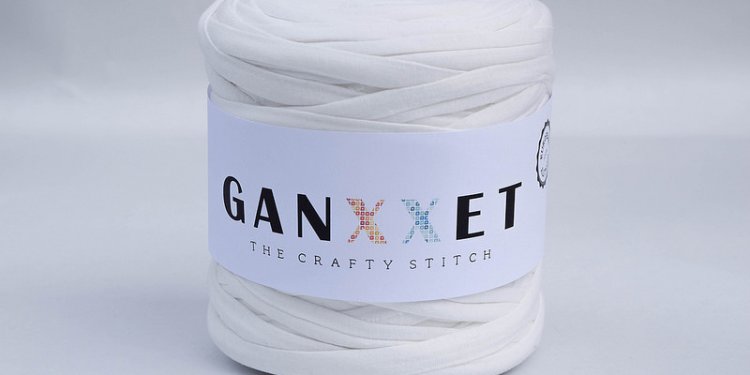
Cotton elastane fabric
[0001]
This application claims priority under 35 U.S.C. §119 to provisional application Ser. No. 61/873, 413 filed Sep. 4, 2013, which application is hereby incorporated by reference in its entirety.
- FIELD OF THE INVENTION
[0002]
This invention is related to a method of manufacturing a cotton weft knit fabric that is resistant to fraying, curling, and laddering.
- BACKGROUND
[0003]
It is well recognized that unrelaxed knitted cotton fabric exhibits a distinct tendency to curl and/or fray at the edges due to unbalanced structures at the face and the back sides of the knitted fabric (See, e.g., Hamilton, R. J., & Postle, R., Bending and recovery properties of wool plain-knitted fabrics, (1974) Textiles Research Journal, 44, 336-343; Spencer, D., Knitting technology (2001), Cambridge: Woodhead). It is theorized that a knitted fabric curls and/or frays when cut because of elastic stored energies in the fabric in terms of bending and torsion. (See Basiri, et al., A new approach to de-curling force of single jersey weft-knitted fabric, Journal of The Textile Institute, 2008). It is theorized that during the curling and/or fraying process, these energies are released.
[0004]
In general in traditional weft knitted fabric, the cut edges are raw edges which tend to curl, ladder, and fray because nothing holds the wales together along the edge once the fabric has been cut.
[0005]
Thus, in traditional weft knitted garments, to prevent this fraying and curling, post-cutting edge treatments such as sewing with over locking stitches, sewing the cut edges together with additional material such as lace, rubber material etc., and/or performing thermal treatments are performed. These additional steps require additional materials, man power, and several processing steps adding additional costs to the garment manufacturing process.
[0006]
Additionally, when hemming is used to treat the cut edges in traditional weft knit garments, the area in the vicinity of the hemming will be pressed and rubbed by the wearer of the garment. This is often uncomfortable for the wearer since the area of the hemming is of a different thickness and texture than the other surfaces of the garment.
[0007]
Therefore, creating a weft knitted cotton-based fabric that resists the tendency to curl and/or fray at the cut edge would be a beneficial invention with many practical applications in the garment manufacturing industry. Such a fabric would ideally be comfortable, would provide a good aesthetic appearance, and because fewer additional treatments would be necessary during the manufacturing process, would be more cost effective than traditional cotton-based garment manufacture.
- DESCRIPTION OF THE FIGURE
[0008]
FIG. 1. Flowchart of an embodiment of the present invention.
- DETAILED DESCRIPTION OF THE PREFERRED EMBODIMENTS
[0009]
The objectives of this invention are to resolve above-highlighted problems with traditional cotton-based weft knitted fabrics and, more specifically, to produce a weft knit cotton-based fabric that does not require hemming even after the fabric is cut into desired shapes. Many studies were conducted and many trials were performed in order to find a way to prevent curling and fraying in cotton-based weft double knit fabric. The fabric of the present invention resists fraying, laddering, and curling and is comfortable for the wearer. The present invention relates to materials, processes, and the associated technologies used to enhance the anti-curling, anti-fraying, and anti-laddering properties of cotton-based weft knitted fabrics.
[0010]
To generate the fraying and curling resistant fabric of the present invention, most preferably, world superior long staple cotton fibers, preferably of a length greater than 30 mm, are used to create a very fine (60ne-100ne) cotton yarn with a high twist factor between about 3.2 and about 4.0. The high twist factor helps to minimize loose fibers in the yarn. Most preferably, the very fine cotton yarn has a count of between about 60ne and about 100ne. Alternatively, regenerated cellulose yarn such as rayon, modal, or viscose or natural yarn such as wool and silk can be used as the very fine yarn. By using very fine yarn, the aesthetic appearance of the fabric is enhanced, as is its value.
[0011]
A secondary fiber yarn is fed together with the very fine cotton yarn in an interlock knitting machine so as to create double knit fabric loops formed by the very fine non-elastic yarn (cotton) on both the external and internal surfaces of the fabric, while the loops created by the secondary fiber (preferably elastane (also known as spandex)) are arranged on both inner surfaces of the fabric. The secondary fiber yarn most preferably comprises elastane fiber yarn. Other fiber yarns such as elaspan, Lycra®, or a similar-type fiber yarn can also be used as the secondary fiber. The linear mass density of the secondary fiber is preferably between about 17—about 44 decitex and is most preferably between about 22 decitex—about decitex.
[0012]
The very fine cotton yarn is fed in parallel with the secondary yarn in an interlock knitting machine. This interlock knitting process allows the secondary fiber yarn to form its loops on the inner side of the double jersey fabric and the very fine cotton yarn to form its loops on the external surfaces of the double jersey fabric.
[0013]
The yarn feeding tension should be adjusted to make stable conditions, so that knit fabric can be knitted with constantly adjusted yarn feeding tension.