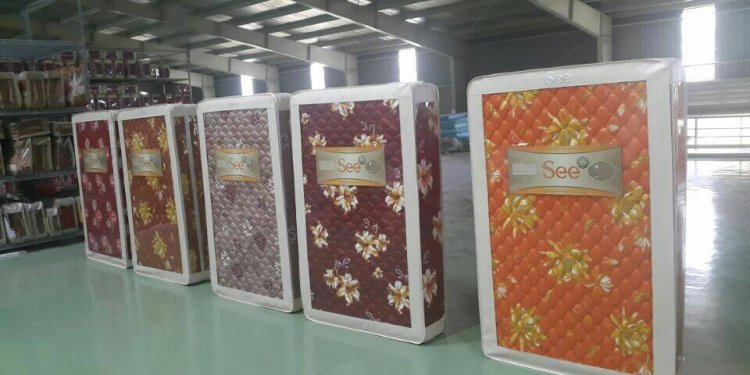
Polyester Fiber Manufacturers
The Manufacturing
Process
Polyester is manufactured by one of several methods. The one used depends on the form the finished polyester will take. The four basic forms are filament, staple, tow, and fiberfill. In the filament form, each individual strand of polyester fiber is continuous in length, producing smooth-surfaced fabrics. In staple form, filaments are cut to short, predetermined lengths. In this form polyester is easier to blend with other fibers. Tow is a form in which continuous filaments are drawn loosely together. Fiberfill is the voluminous form used in the manufacture of quilts, pillows, and outerwear. The two forms used most frequently are filament and staple.
Polymerization
- 1 To form polyester, dimethyl terephthalate is first reacted with ethylene glycol in the presence of a catalyst at a temperature of 302-410°F (150-210°C).
- 2 The resulting chemical, a monomer (single, non-repeating molecule) alcohol, is combined with terephthalic acid and raised to a temperature of 472°F (280°C). Newly-formed polyester, which is clear and molten, is extruded through a slot to form long ribbons.
Drying
- 3 After the polyester emerges from polymerization, the long molten ribbons are allowed to cool until they become brittle. The material is cut into tiny chips and completely dried to prevent irregularities in consistency.
Melt spinning
- 4 Polymer chips are melted at 500-518°F (260-270°C) to form a syrup-like solution. The solution is put in a metal container called a spinneret and forced through its tiny holes, which are usually round, but may be pentagonal or any other shape to produce special fibers. The number of holes in the spinneret determines the size of the yarn, as the emerging fibers are brought together to form a single strand.
- 5 At the spinning stage, other chemicals may be added to the solution to make the resulting material flame retardant, antistatic, or easier to dye.
Drawing the fiber
- 6 When polyester emerges from the spinneret, it is soft and easily elongated up to five times its original length. The stretching forces the random polyester molecules to align in a parallel formation. This increases the strength, tenacity, and resilience of the fiber. This time, when the filaments dry, the fibers become solid and strong instead of brittle.
- 7 Drawn fibers may vary greatly in diameter and length, depending on the characteristics desired of the finished material. Also, as the fibers are drawn, they may be textured or twisted to create softer or duller fabrics.
Winding
- 8 After the polyester yarn is drawn, it is wound on large bobbins or flat-wound packages, ready to be woven into material.
Manufacturing Staple Fiber
In making polyester staple fiber, polymerization, drying, and melt spinning (steps 1-4 above) are much the same as in the manufacture of filament yarn. However, in the melt spinning process, the spinneret has many more holes when the product is staple fiber. The rope-like bundles of polyester that emerge are called tow.
Drawing tow
- 1 Newly-formed tow is quickly cooled in cans that gather the thick fibers. Several lengths of tow are gathered and then drawn on heated rollers to three or four times their original length.
Crimping
- 2 Drawn tow is then fed into compression boxes, which force the fibers to fold like an accordion, at a rate of 9-15 crimps per inch (3-6 per cm). This process helps the fiber hold together during the later manufacturing stages.
Setting
- 3 After the tow is crimped, it is heated at 212-302°F (100-150°C) to completely dry the fibers and set the crimp. Some of the crimp will unavoidably be pulled out of the fibers during the following processes.
Cutting
- 4 Following heat setting, tow is cut into shorter lengths. Polyester that will be blended with cotton is cut in 1.25-1.50 inch (3.2-3.8 cm) pieces; for rayon blends, 2 inch (5 cm) lengths are cut. For heavier fabrics, such as carpet, polyester filaments are cut into 6 inch (15 cm) lengths.