
How to weave fabric on a loom?
When my grandmother taught me how to weave, I had an epiphany about how grainlines and bias impact garment sewing. Suddenly, I understood why it’s so important to match grainlines, why you can get away with cutting some pieces cross-grain but not others, and why the same pattern, if made up in fabrics that are cut in different directions, will result in garments that behave so differently. My garments began to hang better, and I learned several tricks for compensating for fabrics that are off-grain.
When I started teaching sewing, I took this little loom with me to help my students understand the importance of grainlines. Once you connect the weaving process with the final fabric, you will understand enough about woven fabrics to make better garments.
This tiny loom was sold as a toy in the 1950s and has miniature versions of all the working parts you need to see how weaving works.
The Weaving Process
Understanding the weaving process is the first step towards learning about fabric properties.
Fabric starts with the warp. The threads that form the lengthwise grain of the fabric are called the warp threads. These threads are tied onto the loom before weaving begins, and are held taut throughout the weaving process. The warp threads pass through heddles, which can lift specific threads as a group.
In weaving, the crosswise threads are called the weft (also called the woof, especially in older sources). Woven fabric forms as the warp and weft interlock to hold the threads in place. The weaver (or the machine in a modern factory) uses the heddles to raise certain warp threads so that there’s a path between them for the weft to pass through.
In this case, and for all plain-weave fabrics, every other thread is raised. When the weft passes through, it has the same effect as the weaving you may have done as a child where you used a needle to weave yarn over-under-over-under a warp, but this is much more efficient.
The beater tamps the new weft thread against the fabric-in-progress. By moving the heddles in the opposite direction before the weft passes back through, the opposite warp threads are raised, locking each pass of the weft in place and forming the structure of the fabric.
The selvedges are the lengthwise edges of the fabric. As the weft is passed back and forth, it encloses the threads on either side of the warp, forming an integrated edge that won’t unravel. In many commercial fabrics, slightly different threads are used for the selvedges, which can help keep the sides of the fabric taut as its woven.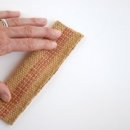
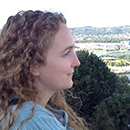