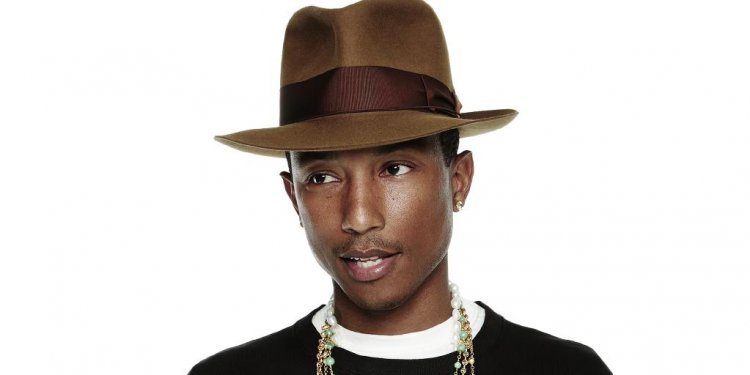
Polyester manufacturing process
Acsis worked with a global manufacturer in order to deliver a solution to bring the manufacturing operations of their polyester films division from a custom based point solution to a productized enterprise data collection platform that they could tightly integrate into their SAP ERP system. The customer is one of the world’s largest manufacturers of polyester films used in ID and security badges, window coatings, food packaging, medical face shields and a wide range of other products. The films are used by the construction, electronics, healthcare, and printing and recording industries, and the specifications for each of these different applications vary widely. Films need to be manufactured in a number of thicknesses, with specialized characteristics – such as heat sealable, printable, laser-engraving capable, etc. – and with unique coatings.
Manufacturing polyester films to critical and varying specifications require complex and precisely controlledprocesses that must be monitored and recorded at every step. Precise tolerances must be verified and recorded from the time a polyester base is extruded on a casting drum and then drawn and stretched under tightly controlled tension and temperature in a multi-zoned oven to achieve the correct film attributes for each batch.
Each plant in this division operates multiple manufacturing lines around the clock, producing both bulk films as well as custom orders for specific customers. They all used a one-off, customized legacy system created and modified over the years primarily for materials management. However, the parent company wanted the division to transition to an SAP structure, bringing it in line with the company’s other divisions worldwide.
BUSINESS CHALLENGES
The legacy system was not set up to integrate with SAP. It was developed and custom coded over time, in piecemeal fashion, in response to changing manufacturing needs and not with the goal of integrating with a standard ERP platform like SAP.
For data collection, the film division needed to look outside the standard SAP modules for a new solution tailored to their needs. That solution also needed to be deployed quickly and cost-effectively to additional plants within the same division, and needed to collect and integrate data into SAP automatically during every step in the manufacturing process – from raw materials receipt to shop-floor manufacturing processes through to finished goods on a 24/7 basis. In the event of SAP going offline, for whatever reason, the solution needed to continue collecting and storing data from all points in the system until SAP was back online.
WHY ACSIS …
Through its successful past work with multiple Fortune 100 companies, Acsis already had a proven track record of crafting highly-efficient, automated data collection solutions that could be fully integrated with SAP and other ERP platforms.
Acsis was selected because the end-to-end solution proposed offered a more efficient and more reliable data collection solution that:
- Assured seamless integration with the new SAP platform;
- Allowed operations when the SAP system or the wide area network was unavailable;
- Provided a store and forward platform to manage the data until the SAP service was available; and
- Could be leveraged easily and cost-effectively at each of the division’s other plants.
THE SOLUTION
Acsis used its Edge platform (formerly VisiTrak®), and the rich library of Acsis transaction sets, to implement an end-to-end, automated data collection solution to track all materials and manufacturing processes from the receiving dock through finished goods. Acsis Edge integrates real-time data from multiple manufacturing lines and multiple staging and post-production areas captured from mobile handheld computers and other shop floor devices into the customer’s SAP system in real time.
Acsis Edge is an ERP add-on, or Edge, solution that adds key functionality to ERP systems, and provides for automated data collection, task and resource management and warehouse management capabilities. It can be configured to post to an ERP system either in real-time or upon task completion.
The Acsis solution gives real-time visibility across the entire manufacturing and warehousing process for better management of time, materials and labor. It also automates data collection as a part of core processes rather than as an afterthought, which can lead to greater accuracy.
Identification labels with barcodes for materials and parts are generated at the receiving dock using wireless barcode printers integrated into the Acsis solution. Then, as material rolls move through the manufacturing, post-production, and warehousing processes, the identifiers are scanned automatically during any pick and put away operations.
Real-time data from integrated shop floor equipment feeds directly into the Edge data collection software and, in turn, feeds into the SAP system in real time, keeping it always up to date. If SAP were to go offline for any reason, Acsis Edge continues to collect transactions from the shop floor and store them locally until the SAP system comes back online.
BENEFITS
Through the Acsis Edge solution, the customer has a single integrated platform for both materials management and manufacturing. This single platform tracks, records and reports real-time data from its complex processes across multiple lines and staging areas and immediately feeds that data into SAP. When SAP is down, data collection continues and data is stored locally until SAP comes back online. This enables the customer to gain real-time visibility over multiple production lines and manufacturing operations, increase operating efficiency, and maintain their 24/7 data collection capability.
By using Acsis’ large library of proven transaction sets in developing this solution, only minor custom coding by Acsis was required. This reduced the customer’s cost of development and implementation, and shortened the overall time required to complete the project. It also made it very cost effective to deploy this standardized solution beyond to additional company locations, providing significant cost savings and efficiencies worldwide.