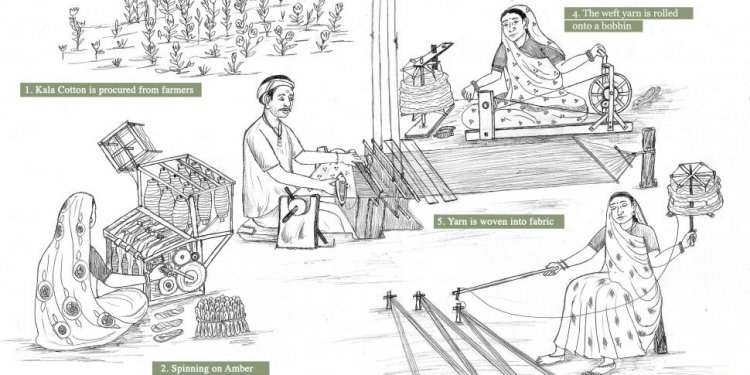
Process of Making cloth from cotton
Based on a flow diagram contained in the book Job Descriptions for the Cotton Textile Industry, June 1939, United States Government Printing Office, Washington. In some steps of the flow diagram, both an "old style" and "new style" process is discussed. Only the old style steps are included below since they would have been used in the late 1800s and early 1900s.
The manufacture of cotton cloth is a complex process, involving many highly skilled workers, each performing a particular critical step in the overall process. The many complex steps can be divided into three general categories - Preparation, Spinning, and Weaving. In addition to this, there is the process of preparing the design that will be applied to the woven cloth. Cotton cloth manufacturing was indeed a "high-tech" venture in the 1880s!
PREPARATION
1. Bales of cotton of various grades are moved from the WAREHOUSE to the BALE OPENING room.
2. Selected bales are opened and placed in position beside the BREAKING and OPENING machine. This is actually a line of machines, working as a unit, that tear apart and partially clean matted, compressed, and baled cotton. The result is small loose bunches of cotton.
3. The cotton is then placed into the BLENDING MACHINE. This is a group of devices that are synchronized to proportion definite amounts of various grades of cotton which are to be blended together.
4. At this time, matted cotton and waste yarn salvaged from operations in the mill are placed into the WASTE MACHINE. This machine beats, pulls apart, and fluffs up waste cotton to prepare it for re-use.
5. Cotton from both the BLENDING MACHINE and the WASTE MACHINE is fed into the BREAKER PICKER. In this unit the raw cotton is partially cleaned by beating and fluffing and then fed into the FINISHER PICKER.
6. The FINISHER PICKER receives partially cleaned cotton in the form of LAP from the BREAKER PICKER and completes the cleaning and fluffing process. LAP is a general term used to designate wide sheets of loosely matted cotton.
7. The cotton is next processed by a CARDING MACHINE, where dirt and short fibers are removed, other fibers are laid parallel and formed into a ropelike strand called a SLIVER. The SLIVER is deposited in large cylindrical containers called CANS.
8. Subsequent processing depends on whether better grade (combed) yarn, or lower grade (carded) yarn is desired. For the lower grade, processig continues at the DRAWING FRAME (see step 12 below)
9. For better grade yarn, the SLIVER is first processed by the SLIVER LAPPING MACHINE, which draws and combines several strands of SLIVER into a sheet of LAP and winds it on a spool ready for RIBBON LAPPING or COMBING.
10. The LAP is processed by a RIBBON LAPPING MACHINE which draws and combines several rolls of LAP into one roll of RIBBON LAP, straightening the fibers slightly and making the lap more uniform in weight and texture, ready for feeding to a COMBING MACHINE. RIBBON LAP is a roll of closely matted cotton fibers, about 10 inches wide.
11. COMBING is the process of extracting fibers below a predetermined length and removing any remaining dirt. Output of the COMBING MACHINE is deposited in CANS.
12. The cotton is next processed by the DRAWING FRAME. It is a machine in which several strands of SLIVER are combined into one strand and DRAWN OUT so that the combined strands approximate the weight and size of any one of the original strands. The term DRAWN OUT means to stretch a strand of cotton, usually by running the strand between several pairs of rollers, each pair turning faster than the pair before it.
13. The SLUBBING MACHINE then draws out strands of SLIVER and twists them together loosely in order to give the strands (now called ROVING) sufficient strength to withstand subsequent operations.
14. The ROVING is processed by the FLY FRAME. This machine progressively combines two strands of partially processed ROVING into one, draws out the combined strands until they are of prescribed weight, and twists them loosely in order to give them sufficient strength to withstand subsequent operations.
SPINNING
1. The cotton is now ready for SPINNING. Spinning is the process of making YARN from cotton fibers by drawing out and twisting the fibers into a thin strand. That is, one or more strands of slightly twisted ROVING are used to produce one strand of spun YARN. The yarn is wound on bobbins.
2. The next step is to produce either WARP or FILLING. WARP is the set of yarn strands which run lengthwise in a piece of cloth. FILLING, also called WOOF and WELT, is the yarn which is interlaced through the WARP to produce cloth.
Making FILLING:
a. FILLING may be single-ply or multiple-ply. For multiple-ply, steps (a) and (b) for making WARP below are completed before the yarn is conditioned. For single-ply, the yarn is immediatly conditioned after spinning. Conditioning is the act of exposing bobbins of FILLING YARN to steam or to a spray of conditioning solution in order to set the twist, to remove kinks from the yarn, and to prevent its kinking in subsequent processes.
Making WARP:
a. The DOUBLING MACHINE winds two or more strands of yarn onto one PACKAGE without twisting them. PACKAGE is simply a general term for any wound arrangement of YARN.
b. The yarn is then TWISTED. The TWISTING MACHINE twists two or more strands of spun yarn into a heavier, stronger, single strand. This process may be repeated until the desired number of plys is produced.
c. The WINDING MACHINE winds yarn from several bobbins in a continuous length onto a spool. Output is CHEESES or CONES of yarn to be used for WARP. The term CHEESE refers to a roll of yarn built up on a paper or wooden tube in a form that resembles a bulk cheese. A CONE is a tapered cylinder of wood, metal, or cardboard around which yarn is wound.
3. The WARP may, or may not, be dyed. If not, then it is next processed by the WARPING MACHINE. This machine takes about 500 strands of yarn and winds them side by side onto one large spool called a SECTION BEAM. The SECTION BEAM is about three feet in diameter. Processing continues at step 6 below.
4. If the WARP is to be dyed, it is processed by the BALL WARPING MACHINE. This machine takes about 500 strands of yarn and gathers them together into a large, loose, rope-like strand, and winds it on a wooden core preparatory to dyeing. The yarn is then dyed in a different location, producing rolls of dyed WARP YARN.
5. The dyed yarn is processed by the BEAMER MACHINE which separates the individual strands of dyed yarn and winds them onto one large spool (BEAM). The result is the same as step 3 above.
6. The SLASHING MACHINE takes the yarns from several SECTION BEAMS and winds them side by side onto one wider spool called a LOOM BEAM.
WEAVING
1. WEAVING is the interlacing of WARP and FILLING YARN to form a cloth.
1. The inputs to the weaving process, performed on a LOOM, are (1) the WARP YARN from the LOOM BEAM (2) the FILL YARN from a bobbin, and (3) the mechanism that controls the design to be applied to the cloth (see Designing below).